Zero Emission Rehab ®

Forward-Thinking Solutions
The IBG HydroTech "Zero Emission Rehab®" Trenchless Pipe Rehabilitation System
For over 25 years, IBG HydroTech GmbH has been at the forefront of developing hydrodynamic pipe cleaning and trenchless rehabilitation systems. Our latest innovation, the "Zero Emission Rehab®," marks a significant leap towards a sustainable future in pipe rehabilitation. Over the past three years, we've expanded our product line to include electrically powered equipment, aiming to create zero-emission job sites.
Starting with the first battery-powered robotic systems, our "Zero Emission Rehab®" label now encompasses a full range of E-products designed to meet the highest environmental standards. But we don't stop at just the equipment. IBG HydroTech GmbH considers the entire ecosystem—from charging infrastructure and service offerings to financing options and diverse usage models. We even take into account the lifecycle of the batteries we use.
In line with this forward-thinking strategy, we're proud to offer our patented IBG UV Curing System with the Zero Emission Rehab® standard. This system ensures zero-emission UV liner rehabilitation sites without compromising on performance or increasing costs.
Benefits for Municipalities, Contractors, and Engineering Firms
Our zero-emission technology brings significant advantages to municipalities, residents, industrial clients, engineering firms, and construction companies.
Embrace the future of trenchless pipe rehabilitation with IBG HydroTech's "Zero Emission Rehab®" system and join us in making a positive impact on our environment.
Emission-Free
Operation During UV Liner Curing
Power Supply
Powered by the IBG Performance Battery with a capacity of 45 kWh, offering 6-10 hours of operation.
Energy Management
Equipped with energy management software, including a charging system and inverter.
CO2 Footprint
Reduces CO2 emissions by at least 80%.
Transport Vehicles
Uses two 3.5-ton carrier vehicles (drivable with a standard license) without the need for trailers.
Leak Detection
Immediate identification of leaks in the liner film.
Reliability
Reduces the risk of failure associated with generators or blowers.
Optional Air Supply
Can be filled with filtered air from pressure tanks (300 bar - approximately 18 m³ per tank; DN300 = 100 meters = 7 m³).
Emission-Free Operation
Maintains zero-emission operation during UV manhole curing.
Logistics and Travel Time
Reduced logistics and travel time (no 80 km/h speed limit).
Reduced Costs
Lower personnel and transport costs (no toll fees).
Operational Efficiency
Shortens operational site times.
Cost Savings
Reduces both CAPEX (Capital Expenditure) and OPEX (Operational Expenditure).
Sustainable Energy
Utilizes sustainable charging power.
Competitive Advantage
Provides benefits in tender processes with relevant bidding requirements.
Experience the future of trenchless pipe rehabilitation with our emission-free UV liner curing system, designed for maximum efficiency and minimal environmental impact.
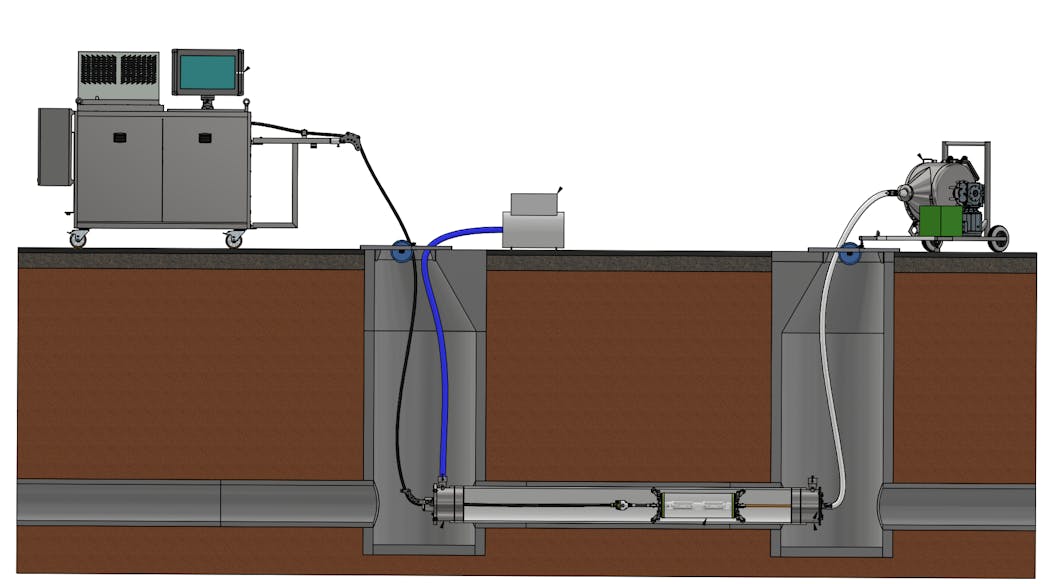
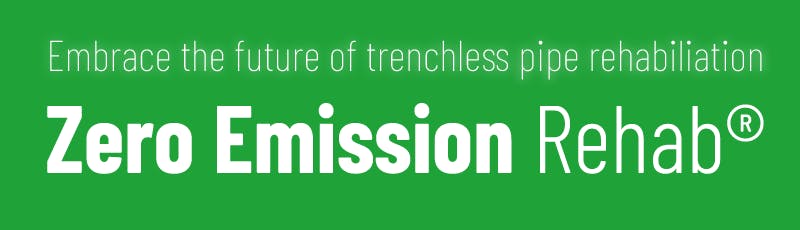